Electronic Grade Ammonia Water
Shanxian Chemical
HS Code |
130970 |
Chemical Formula | NH₃·H₂O |
Appearance | Colorless transparent liquid |
Odor | Pungent ammonia smell |
Density | 0.91 g/cm³ (at 20°C) |
Boiling Point | Around 37.7°C (25% ammonia solution) |
Melting Point | -77.7°C |
Ph Value | Alkaline, usually above 11 |
Solubility | Miscible with water in all proportions |
Flash Point | Non - flammable |
Stability | Decomposes upon heating to release ammonia gas |
Corrosiveness | Corrosive to some metals and materials |
As an accredited Electronic Grade Ammonia Water factory, we enforce strict quality protocols—every batch undergoes rigorous testing to ensure consistent efficacy and safety standards.
Packing | Electronic Grade Ammonia Water, 5 - liter plastic bottle packaging. |
Storage | Electronic Grade Ammonia Water should be stored in a cool, well - ventilated area away from heat sources and ignition points. It must be kept in tightly - sealed, corrosion - resistant containers, preferably made of materials like high - density polyethylene. Storage areas should be separate from incompatible substances to prevent reactions and ensure safety. |
Shipping | Electronic Grade Ammonia Water is shipped in specialized, corrosion - resistant containers. Strict safety protocols are followed during transportation to prevent leakage, ensuring compliance with hazardous chemical shipping regulations. |
Competitive Electronic Grade Ammonia Water prices that fit your budget—flexible terms and customized quotes for every order.
For samples, pricing, or more information, please call us at +8615365186327 or mail to info@liwei-chem.com.
We will respond to you as soon as possible.
Tel: +8615365186327
Email: info@liwei-chem.com
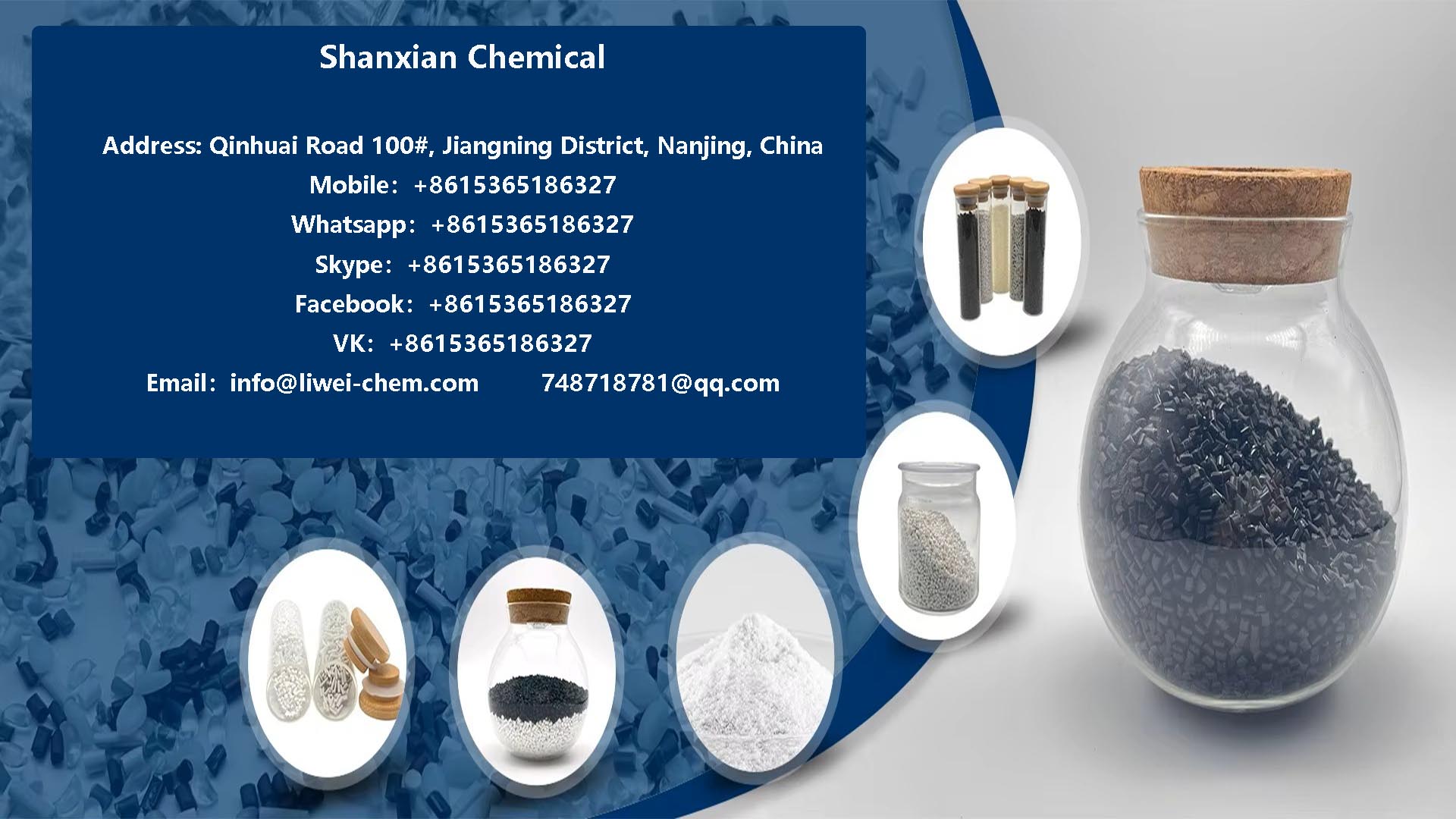
At first, only the properties of ammonia were known, but the wonders of its refined products were not known. After further research and technological progress, Electronic Grade Ammonia Water began to emerge.
In the past, the preparation was difficult and the quality was difficult to control. However, scholars have been unremitting, and there have been repeated innovations in the process. From the goodness of the instrument to the simplicity of the process, there have been improvements.
Since then, the quality of Electronic Grade Ammonia Water has gradually improved, and its use has also become more and more widespread. From the field of electronics to all kinds of chemicals, it all depends on its strength. Looking at the path of its development, it really depends on the wisdom and diligence of researchers of all dynasties to achieve today's prosperity.
This product has precise concentration and good stability. It can be applied to chip etching, electronic component cleaning and other things. The preparation method combines the ingenuity of modern chemical industry, layers of fine filtration, and heavy purification to obtain this high-purity product.
Use it, the performance of electronic devices can be excellent, and defects can be eliminated. It is essential to the electronics industry, like water to boats, and is indispensable. It is a treasure in the field of electronic manufacturing, helping the industry to move forward vigorously.
It has a wide range of uses in the electronic field. Due to its extremely high purity requirements, the physical and chemical properties must be controlled very precisely. Insufficient purity and the presence of impurities are very harmful to the manufacture of electronic components, resulting in poor performance and even component damage. Therefore, researchers continue to study its physical and chemical properties in order to improve quality and meet the increasingly demanding needs of the electronics industry, so that it can be used in electronic manufacturing and help the industry thrive.
Looking at this product, the first purity of the technical specifications must reach a very high standard, and the impurities must be minimal before it can be applied to the precise needs of the electronic field. And its pH, conductivity and other parameters must also be precisely controlled.
In terms of identification, the product parameters should be clear in the packaging, such as concentration geometry and application range. In this way, users can make good use of it according to their needs. Strict adherence to technical specifications and accurate marking is essential to ensure the quality of Electronic Grade Ammonia Water, which has been a great success in the development of the electronics industry.
In the reaction, it either acts as a medium or a reactant, which affects the direction and speed of the reaction. When modified, it can adjust its molecular structure and change its physical and chemical properties to meet diverse needs.
Chemists should study the rules of reaction of this product, investigate its modification methods, and use ancient theories to integrate modern science and technology, so that this product can be used in various fields of industry and scientific research to develop its growth, and to increase its benefits.
Or "high purity ammonia", because of its high purity, it is very much in demand in fine industries such as electronic manufacturing, and high purity is its key characteristic, so the name is obtained.
It is also called "ultra-pure ammonia water", and the word "super" shows its extreme purity. Compared with ordinary ammonia water, there are almost no impurities, so it can meet the strict requirements of the electronic industry for ultra-high purity of materials. All other names are based on the different application scenarios and quality characteristics of this product, but they all refer to Electronic Grade Ammonia Water.
Covers the principle of all things, safety comes first; the rules of operation, follow the law. In today's words, electronic grade ammonia is widely used in various industries, but its nature is special, it is related to safety, and it cannot be ignored.
Electronic grade ammonia is highly corrosive, touches the skin, and immediately sees damage. Therefore, those who use this thing must wear protective gear. If it is protective clothing, protective gloves, anti-goggles, etc., make sure that the whole body is complete and there is no omission.
Store it in a cool and dry place, away from fire and heat sources. Because it is volatile, and the volatilized ammonia is flammable and toxic, if you are not careful, you may risk fire, explosion, or poisoning.
When operating, the action should be slow and do not splash the liquid. If there is a splash, rinse it with a lot of water quickly, and in severe cases, seek medical diagnosis and treatment. The method of mixing the liquid should follow the precise recipe, and do not change the ratio at will to prevent abnormal reactions.
Furthermore, the system of ventilation is crucial. There must be good ventilation equipment in the operation room, so that the volatilized ammonia can be quickly discharged outside, so as not to gather in the room and endanger everyone.
All of these are the main rules for the safety and operation of electronic-grade ammonia. Practitioners should keep it in mind and abide by it, so as to ensure that everything goes smoothly and is safe.
In the manufacture of display panels, it is also indispensable. It can clear the impurities on the screen surface, keep the pixels clear and the picture is bright.
In the preparation of optoelectronic materials, it can adjust the reaction environment and promote the synthesis of materials. It makes the material of good quality and excellent photoelectric properties.
All these ends show the importance of Electronic Grade Ammonia Water in the application field. It contributes to the development of the modern electronics industry and is indispensable.
Then he devoted himself to consulting ancient books and this book, and studying all kinds of skills. In the selection of raw materials, it is necessary to seek high-quality; in the regulation of the process, it is necessary to investigate every detail. After months of research and experimentation, I have gradually obtained exquisite methods. The Electronic Grade Ammonia Water made has greatly reduced impurities, increased purity, and good quality.
However, the road to research is endless, and it is still necessary to expand its application scope and improve performance. We hope to work together with all colleagues to make this product stand out in the electronics industry, promote the progress of the industry, and achieve long-term development.
At present, the electronics industry is booming, and the demand for high-purity materials is increasing day by day. Electronic Grade Ammonia Water, with its excellent performance, can adapt to the strict requirements of electronic manufacturing, helping its device performance to improve and quality to be solid.
Looking forward to the future, the progress of science and technology has no end. Electronic devices must be more refined, smaller and stronger. Electronic Grade Ammonia Water will also be refined, and will be able to reach a higher level in terms of purity improvement and impurity control. And its application scope will also be expanded to emerging electronic fields, such as quantum chips, flexible electronics, etc., adding to the prosperity of the future electronics industry and becoming an indispensable item.
As a leading Electronic Grade Ammonia Water supplier, we deliver high-quality products across diverse grades to meet evolving needs, empowering global customers with safe, efficient, and compliant chemical solutions.
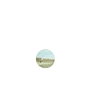
Scan to WhatsApp