Halogen-Free Flame Retardant Masterbatch
Shanxian Chemical
HS Code |
910645 |
Flammability | Highly flame - retardant |
Halogen Content | Zero |
Thermal Stability | Good, withstands high processing temperatures |
Mechanical Properties Tensile | Maintains good tensile strength |
Dispersion Ability | Excellent dispersion in polymers |
Chemical Resistance | Resistant to common chemicals |
Weather Resistance | Good weather - resistance |
Smoke Generation | Low smoke generation during combustion |
Toxic Gas Emission | Low toxic gas emission during combustion |
Compatibility | Good compatibility with various polymers |
As an accredited Halogen-Free Flame Retardant Masterbatch factory, we enforce strict quality protocols—every batch undergoes rigorous testing to ensure consistent efficacy and safety standards.
Packing | Halogen - Free Flame Retardant Masterbatch, 25 - kg bags for safe and easy handling. |
Storage | Halogen - Free Flame Retardant Masterbatch should be stored in a cool, dry place away from direct sunlight and heat sources. Keep it in a well - ventilated area to prevent moisture absorption. Store in original packaging to maintain its quality. Avoid contact with incompatible substances. Proper storage helps preserve its flame - retardant properties and ensures safety during storage. |
Shipping | Halogen - Free Flame Retardant Masterbatch is shipped in sealed, sturdy containers to prevent moisture and contamination. Shipment may be via road, sea, or air, adhering to strict chemical transportation regulations. |
Competitive Halogen-Free Flame Retardant Masterbatch prices that fit your budget—flexible terms and customized quotes for every order.
For samples, pricing, or more information, please call us at +8615365186327 or mail to info@liwei-chem.com.
We will respond to you as soon as possible.
Tel: +8615365186327
Email: info@liwei-chem.com
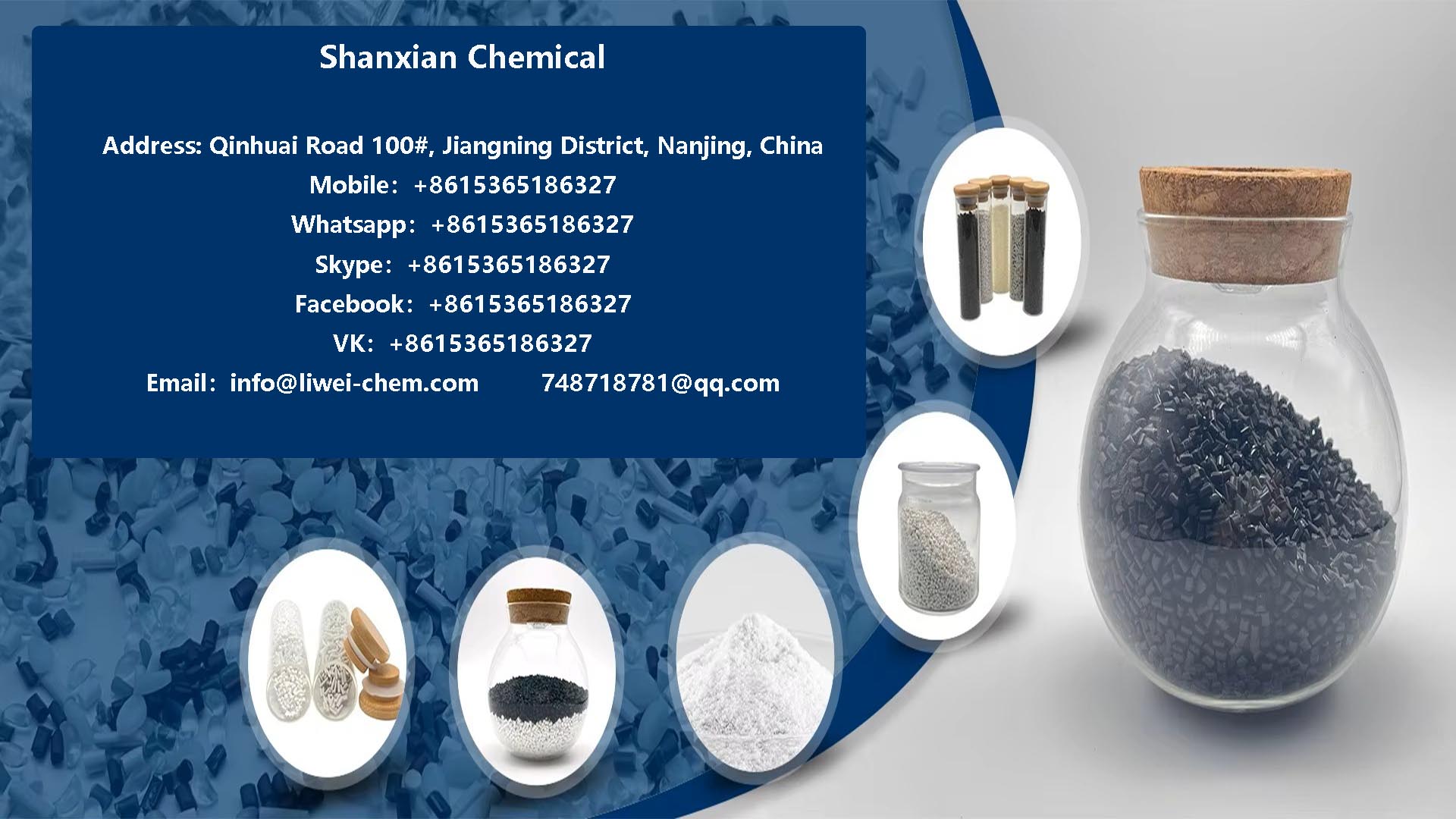
Then we thought of innovation and developed halogen-free flame retardant masterbatches. At the beginning, the road of exploration was full of thorns, and the performance indicators were difficult to meet expectations. However, after years of menstruation, we worked hard on raw material selection, formula modulation, process optimization, etc. Gradually, halogen-free flame retardant masterbatch was invented, which has the advantages of flame retardant, high efficiency, environmental protection and non-toxicity. It meets the needs of the times and has emerged in many fields, opening a new chapter of flame retardant materials for future generations.
This product does not have halogen ingredients and conforms to the general trend of environmental protection. It is not only halogen-free, but also highly flame retardant and ensures material safety. Its performance is stable, temperature and weather resistance, and good compatibility with various substrates, without damaging the original properties of the material. It is widely used in rubber, plastics, fiber and other industries, and can greatly improve the flame retardant grade of materials, protect the safety of people and property, and is also a good product in the field of chemical flame retardant.
The physical and chemical properties of halogen-free flame retardant masterbatch are unique. Its thermal stability is good, and it is not easy to decompose in high temperature environment, which can ensure the stable performance of the material during processing and use. And it has good compatibility with a variety of polymer materials, and it is evenly dispersed without damaging the original mechanical properties of the material. In terms of chemical structure, it contains flame retardant elements such as phosphorus and nitrogen, which exert flame retardant efficiency through mechanisms such as dehydration and Its flame retardant efficiency is high, and a small amount of addition can significantly enhance the flame retardant grade of the material, providing a strong guarantee for the fire safety of the material. It has broad prospects in today's material field.
Halogen-free flame retardant masterbatch technical specifications need to clarify the composition to ensure halogen-free and efficient flame retardant. Its flame retardant performance indicators, such as oxygen index, should meet specific standards to ensure effective flame retardant in different scenarios. Thermal stability is also critical, and it needs to withstand high temperatures during processing.
In terms of identification, the product label should clearly indicate "Halogen - Free Flame Retardant Masterbatch", and detail parameters, such as ingredient ratio, applicable materials, so that customers can accurately grasp product characteristics, ensure product compliance and meet the requirements of use, in order to meet the market demand for environmentally friendly flame retardant materials.
Its production process, first prepare the raw materials according to a specific ratio. Then mix evenly with a high-speed mixer to make the ingredients blend. Then melt blending and granulation through a twin-screw extruder, and rotate with a screw to achieve good dispersion and plasticization.
The reaction step is also required. When the raw materials are mixed, the molecules interact, melt blending, chemical bond recombination, and give the product excellent performance. In this process, temperature control, speed control, and reasonable reaction conditions are set to ensure product quality.
In addition, a quality monitoring mechanism is established to check in all links to ensure that the product meets standards. In this way, high-quality halogen-free flame retardant masterbatch can be obtained.
In terms of chemical response, halogen-free flame retardant masterbatch uses elements such as phosphorus and nitrogen to cooperate. When heated, it may dehydrate into carbon, or produce gas to trap oxygen, in order to achieve the effect of flame retardancy. Its response mechanism is exquisite, and it is efficient and low-toxic.
When it comes to modification, the developers use nanotechnology and surface modification methods to increase the compatibility between halogen-free flame retardant masterbatch and matrix materials, improve dispersion, and then strengthen the comprehensive properties of materials. In this way, halogen-free flame retardant masterbatch not only has flame retardant ability, but also does not damage the original characteristics of the material, and has broad prospects for industry and people's livelihood.
Halogen-free flame retardant masterbatches are widely used in this world. It is related to safety and operation regulations and cannot be ignored.
In the way of storage, it must be placed in a cool, dry and ventilated place. Avoid direct sunlight and avoid rain. This is due to the intensity of sunlight, or the properties of the masterbatch may change; the wetness of rain can also damage its quality. And it should be stored separately from other things to prevent mutual influence and keep it pure.
When taking it, keep your hands and utensils clean. Unclean things mixed in it will damage its quality. The amount should be used according to the needs of the things made, and it should be accurate. Do not overdo it or lack it. If it is too expensive and may cause performance deviation, it will not achieve the effect of flame retardancy.
In the operating environment, air circulation is essential. Due to the presence of odor and dust between operations, the circulating air can be dispersed to protect the health of the operator. And the operator should be in front of protective equipment, such as masks and gloves. The mask can prevent dust from entering the body, and the gloves can avoid the connection between the masterbatch and the skin, and avoid allergies and other diseases.
Furthermore, the cleaning and maintenance of the equipment should not be neglected. After use, the equipment must be cleaned to remove the remaining masterbatch. Otherwise, it will accumulate fouling for a long time, causing the equipment to run poorly, and affecting the effect of the next use.
There are also regulations for disposing of waste. Do not discard them at will, when in accordance with the law of environmental protection, collect them in categories and dispose of them properly.
In this way, strictly abide by the regulations on the safety and operation of halogen-free flame retardant masterbatches, in order to ensure smooth production, protect the safety of personnel, and meet the requirements of environmental protection.
At the beginning, the road to exploration was full of thorns. Raw material screening requires weighing multiple characteristics; process optimization, often repeated trial and error. However, Yu and colleagues are determined to study day and night.
After a long time of hard work, we have finally achieved success. The products made have excellent performance, significant flame retardant effect, and meet the strict standards of environmental protection. This achievement has not only been widely praised in the academic community, but also has a bright future for industrial applications. Looking to the future, we hope to build on this foundation, continue to improve, promote the development of the industry, and contribute to the progress of society.
Halogen-free flame retardant masterbatch, want to replace halogen-based. Examine its ingredients carefully, and choose non-toxic or low-toxic substances, which are made by exquisite proportions and advanced processes. Experiments have shown that its combustion products have less harmful gases and smoke, and do not produce highly toxic hydrogen halides such as halogen-based. Biotoxicity tests also show that its harm to organisms is minimal. Therefore, halogen-free flame retardant masterbatch is at the toxic end, which is significantly better than halogen-based flame retardants, and can be a good choice for safe fire protection. It has broad prospects in the field of material fire protection in the future.
Not yet, with the growing awareness of environmental protection and stricter regulations, traditional halogen-containing flame retardants are gradually being abandoned. This Halogen - Free Flame Retardant Masterbatch is sure to gain more favor. Its application will also be expanded to electronics, textiles, construction and other fields, driving safety and environmental protection in various industries. In this way, its market scale is expected to continue to expand, becoming a bright new star in the flame retardant industry, leading the future change and development of flame retardant materials.
As a leading Halogen-Free Flame Retardant Masterbatch supplier, we deliver high-quality products across diverse grades to meet evolving needs, empowering global customers with safe, efficient, and compliant chemical solutions.
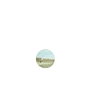
Scan to WhatsApp