Hydrogen Generation Process Key Terms
Hydrogen Production Process
Guidelines for Key Terms of Hydrogen Production Process
The following will focus on the key terms related to hydrogen production process to explain the hydrogen production process.
Feedstock Selection
The primary key to hydrogen production process is the selection of raw materials. Common hydrogen production raw materials include fossil fuels, such as natural gas and coal; there are also renewable resources, such as biomass. Natural gas is rich in methane, which is widely used in steam reforming hydrogen production due to its cleanliness and efficiency. It reacts chemically with water vapor at high temperatures and under the action of catalysts to generate hydrogen and carbon monoxide. While coal gasification for hydrogen production, although the raw material reserves are abundant, follow-up gas purification needs to be paid attention to to to improve hydrogen purity. Biomass hydrogen production is renewable and low-pollution, but the technological maturity needs to be improved.
Chemical Reaction Process
1. ** Steam Reforming Reaction **: Take natural gas steam reforming as an example, this is an endothermic reaction. At high temperatures (usually 700 - 1000 ° C) and nickel-based catalysts, methane ($CH_4 $) reacts with water vapor ($H_2O $) with the chemical equation $CH_4 + H_2O\ stackrel {catalyst} {\ longrightarrow} CO + 3H_2 $. The generated carbon monoxide can be further reacted with water vapor through a transformation reaction to generate more hydrogen and carbon dioxide, namely $CO + H_2O\ stackrel {catalyst} {\ longrightarrow} CO_2 + H_2 $.
2. ** Partial oxidation reaction **: For some carbon-rich feedstocks, partial oxidation can be used. With the participation of an appropriate amount of oxygen, the feedstock is not completely burned, releasing heat to power the hydrogen production reaction. For example, the partial oxidation reaction of natural gas, $2CH_4 + O_2\ stackrel {catalyst} {\ longrightarrow} 2CO + 4H_2 $. This reaction can be carried out at relatively low temperatures and can produce hydrogen quickly.
3. ** Water electrolysis reaction **: When electricity is derived from renewable energy sources, electrolysis of water to produce hydrogen is a very promising way. In the electrolyzer, under the action of direct current, the water is decomposed into hydrogen and oxygen, and the anodic reaction is $2H_2O\ longrightarrow O_2 + 4H ^ ++ 4e ^ - $, and the cathodic reaction is $4H ^ ++ 4e ^ -\ longrightarrow 2H_2 $. This process is pollution-free and the product has high hydrogen purity, but the energy consumption problem needs to be solved by improving the electrolysis efficiency and reducing power consumption.
The gas mixture generated by the gas separation and purification
reaction needs to be separated and purified to obtain high-purity hydrogen.
1. ** Pressure swing adsorption (PSA) **: Separation is achieved based on differences in the adsorption capacity of the adsorbent to different gases and pressure changes. Under high pressure, impurity gases are adsorbed and hydrogen flows out; when pressure is lowered, the adsorbent desorbs impurities. The technology is easy to operate and flexible, and can produce high-purity hydrogen.
2. ** Membrane separation **: Different principles of penetration rates for different gases using special membrane materials. Hydrogen molecules are small and pass through the membrane quickly, enabling separation from other gases. Membrane separation technology has low energy consumption and compact device, but the performance and life of membrane materials affect its application.
3. ** Low temperature separation **: According to the difference in boiling points of each component of the mixed gas, the gas is liquefied by deep freezing, and then fractionated to obtain high-purity hydrogen. This method is suitable for large-scale hydrogen production and requires extremely high hydrogen purity scenarios, but the equipment investment and energy consumption are relatively large.
Process optimization and development trends
1. ** Catalyst improvement **: Develop high-activity, high-stability catalysts with excellent anti-carbon deposition performance to improve reaction efficiency and selectivity, reduce reaction temperature and energy consumption. For example, new nanostructured catalysts can increase the activity check point and enhance the catalytic effect.
2. ** Coupling process **: Coupling multiple hydrogen production processes to learn from each other's strengths. For example, combining steam reforming with partial oxidation to optimize energy utilization and hydrogen production. Or coupling with carbon dioxide capture and storage technology to reduce carbon emissions.
3. ** Intelligent control **: Use advanced automated control and monitoring systems to adjust process parameters in real time to ensure stable and efficient operation of the hydrogen production process. Through big data and artificial intelligence technology, predict equipment failures, maintain in advance, and improve production safety and reliability.
Guidelines for Key Terms of Hydrogen Production Process
The following will focus on the key terms related to hydrogen production process to explain the hydrogen production process.
Feedstock Selection
The primary key to hydrogen production process is the selection of raw materials. Common hydrogen production raw materials include fossil fuels, such as natural gas and coal; there are also renewable resources, such as biomass. Natural gas is rich in methane, which is widely used in steam reforming hydrogen production due to its cleanliness and efficiency. It reacts chemically with water vapor at high temperatures and under the action of catalysts to generate hydrogen and carbon monoxide. While coal gasification for hydrogen production, although the raw material reserves are abundant, follow-up gas purification needs to be paid attention to to to improve hydrogen purity. Biomass hydrogen production is renewable and low-pollution, but the technological maturity needs to be improved.
Chemical Reaction Process
1. ** Steam Reforming Reaction **: Take natural gas steam reforming as an example, this is an endothermic reaction. At high temperatures (usually 700 - 1000 ° C) and nickel-based catalysts, methane ($CH_4 $) reacts with water vapor ($H_2O $) with the chemical equation $CH_4 + H_2O\ stackrel {catalyst} {\ longrightarrow} CO + 3H_2 $. The generated carbon monoxide can be further reacted with water vapor through a transformation reaction to generate more hydrogen and carbon dioxide, namely $CO + H_2O\ stackrel {catalyst} {\ longrightarrow} CO_2 + H_2 $.
2. ** Partial oxidation reaction **: For some carbon-rich feedstocks, partial oxidation can be used. With the participation of an appropriate amount of oxygen, the feedstock is not completely burned, releasing heat to power the hydrogen production reaction. For example, the partial oxidation reaction of natural gas, $2CH_4 + O_2\ stackrel {catalyst} {\ longrightarrow} 2CO + 4H_2 $. This reaction can be carried out at relatively low temperatures and can produce hydrogen quickly.
3. ** Water electrolysis reaction **: When electricity is derived from renewable energy sources, electrolysis of water to produce hydrogen is a very promising way. In the electrolyzer, under the action of direct current, the water is decomposed into hydrogen and oxygen, and the anodic reaction is $2H_2O\ longrightarrow O_2 + 4H ^ ++ 4e ^ - $, and the cathodic reaction is $4H ^ ++ 4e ^ -\ longrightarrow 2H_2 $. This process is pollution-free and the product has high hydrogen purity, but the energy consumption problem needs to be solved by improving the electrolysis efficiency and reducing power consumption.
The gas mixture generated by the gas separation and purification
reaction needs to be separated and purified to obtain high-purity hydrogen.
1. ** Pressure swing adsorption (PSA) **: Separation is achieved based on differences in the adsorption capacity of the adsorbent to different gases and pressure changes. Under high pressure, impurity gases are adsorbed and hydrogen flows out; when pressure is lowered, the adsorbent desorbs impurities. The technology is easy to operate and flexible, and can produce high-purity hydrogen.
2. ** Membrane separation **: Different principles of penetration rates for different gases using special membrane materials. Hydrogen molecules are small and pass through the membrane quickly, enabling separation from other gases. Membrane separation technology has low energy consumption and compact device, but the performance and life of membrane materials affect its application.
3. ** Low temperature separation **: According to the difference in boiling points of each component of the mixed gas, the gas is liquefied by deep freezing, and then fractionated to obtain high-purity hydrogen. This method is suitable for large-scale hydrogen production and requires extremely high hydrogen purity scenarios, but the equipment investment and energy consumption are relatively large.
Process optimization and development trends
1. ** Catalyst improvement **: Develop high-activity, high-stability catalysts with excellent anti-carbon deposition performance to improve reaction efficiency and selectivity, reduce reaction temperature and energy consumption. For example, new nanostructured catalysts can increase the activity check point and enhance the catalytic effect.
2. ** Coupling process **: Coupling multiple hydrogen production processes to learn from each other's strengths. For example, combining steam reforming with partial oxidation to optimize energy utilization and hydrogen production. Or coupling with carbon dioxide capture and storage technology to reduce carbon emissions.
3. ** Intelligent control **: Use advanced automated control and monitoring systems to adjust process parameters in real time to ensure stable and efficient operation of the hydrogen production process. Through big data and artificial intelligence technology, predict equipment failures, maintain in advance, and improve production safety and reliability.
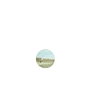
Scan to WhatsApp