Hydrogen Tanks Key Aspects
On Hydrogen Tanks
Hydrogen tanks are important in this world. They are crucial in the field of energy and are related to the future trend, so they are discussed in detail.
First, the material of hydrogen tanks
The material of hydrogen tanks is sturdy and safe. It needs to be able to withstand high pressure and resist hydrogen embrittlement. Common metal materials, such as aluminum alloys, are light in weight and have considerable strength, and can withstand certain pressure. However, their protection against hydrogen penetration still needs to be refined. There are also composite materials, such as carbon fiber reinforced plastics. This material is light and strong, and has good resistance to hydrogen penetration. It is suitable for high-pressure hydrogen storage. It can reduce the weight of the tank and increase the efficiency of hydrogen storage, which is the key to the development of hydrogen tank materials.
Second, the beauty of hydrogen tank design
Design is related to the performance and practicality of hydrogen tanks. First, the shape design needs to be considered. The spherical tank is evenly stressed, can better withstand high pressure, and yet occupies more land. The cylindrical tank is easy to arrange and install, and has its advantages in space utilization. Second, the internal structure design is also critical. Reasonable baffle and diversion devices can make the hydrogen distribution uniform, the charging and discharging process smoother, and improve the overall performance of the hydrogen tank. Furthermore, the connection and sealing design are related to whether hydrogen leaks or not, and must be carefully considered to ensure safety.
III. Safety of hydrogen tanks
Safety is the lifeblood of hydrogen tanks. Hydrogen is flammable and explosive, so the safety protection of hydrogen tanks is the key. First, multiple safety valves are installed, which can automatically relieve pressure in case of abnormal pressure and avoid the risk of tank bursting. Second, a hydrogen leakage monitoring device is installed, which can sense leaks in real time and give timely warnings so that countermeasures can be taken. Third, a fireproof and heat insulation coating is installed on the surface of the tank. In case of fire, it can block heat from entering and ensure the stability of hydrogen in the tank. And during daily operation and maintenance, regular inspections are carried out to ensure that the performance of the hydrogen tank is normal and foolproof.
IV. The essence of hydrogen tank manufacturing
The manufacturing process determines the quality of the hydrogen tank. From material processing to tank molding, all skills are required. Material processing requires precise control of size and performance. During the molding process, welding, winding and other processes must be fine. The welding site needs to ensure strength and sealing, and the carbon fiber winding should be uniform and tight, so that all parts of the tank are under the same force. Strict quality inspection runs through the entire manufacturing process, non-destructive testing, stress testing, etc., to ensure that each hydrogen tank meets high standards and lays a solid foundation for hydrogen energy applications.
Hydrogen tanks are a key tool at the time of energy change. Materials, design, safety, and manufacturing all need to be refined. Only in this way can hydrogen tanks help the wide application of hydrogen energy and promote the clean and sustainable development of energy.
Hydrogen tanks are important in this world. They are crucial in the field of energy and are related to the future trend, so they are discussed in detail.
First, the material of hydrogen tanks
The material of hydrogen tanks is sturdy and safe. It needs to be able to withstand high pressure and resist hydrogen embrittlement. Common metal materials, such as aluminum alloys, are light in weight and have considerable strength, and can withstand certain pressure. However, their protection against hydrogen penetration still needs to be refined. There are also composite materials, such as carbon fiber reinforced plastics. This material is light and strong, and has good resistance to hydrogen penetration. It is suitable for high-pressure hydrogen storage. It can reduce the weight of the tank and increase the efficiency of hydrogen storage, which is the key to the development of hydrogen tank materials.
Second, the beauty of hydrogen tank design
Design is related to the performance and practicality of hydrogen tanks. First, the shape design needs to be considered. The spherical tank is evenly stressed, can better withstand high pressure, and yet occupies more land. The cylindrical tank is easy to arrange and install, and has its advantages in space utilization. Second, the internal structure design is also critical. Reasonable baffle and diversion devices can make the hydrogen distribution uniform, the charging and discharging process smoother, and improve the overall performance of the hydrogen tank. Furthermore, the connection and sealing design are related to whether hydrogen leaks or not, and must be carefully considered to ensure safety.
III. Safety of hydrogen tanks
Safety is the lifeblood of hydrogen tanks. Hydrogen is flammable and explosive, so the safety protection of hydrogen tanks is the key. First, multiple safety valves are installed, which can automatically relieve pressure in case of abnormal pressure and avoid the risk of tank bursting. Second, a hydrogen leakage monitoring device is installed, which can sense leaks in real time and give timely warnings so that countermeasures can be taken. Third, a fireproof and heat insulation coating is installed on the surface of the tank. In case of fire, it can block heat from entering and ensure the stability of hydrogen in the tank. And during daily operation and maintenance, regular inspections are carried out to ensure that the performance of the hydrogen tank is normal and foolproof.
IV. The essence of hydrogen tank manufacturing
The manufacturing process determines the quality of the hydrogen tank. From material processing to tank molding, all skills are required. Material processing requires precise control of size and performance. During the molding process, welding, winding and other processes must be fine. The welding site needs to ensure strength and sealing, and the carbon fiber winding should be uniform and tight, so that all parts of the tank are under the same force. Strict quality inspection runs through the entire manufacturing process, non-destructive testing, stress testing, etc., to ensure that each hydrogen tank meets high standards and lays a solid foundation for hydrogen energy applications.
Hydrogen tanks are a key tool at the time of energy change. Materials, design, safety, and manufacturing all need to be refined. Only in this way can hydrogen tanks help the wide application of hydrogen energy and promote the clean and sustainable development of energy.
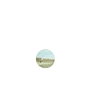
Scan to WhatsApp