Sealing Solutions for Hydrogen Applications
On the sealing solution for hydrogen applications
Hydrogen is unique and increasingly important in today's applications. However, when it is applied, the sealing business is the most critical, and it is related to many important items such as efficiency and safety.
If you want a sealing solution suitable for hydrogen applications, the first thing to understand is the characteristics of hydrogen. Hydrogen has minimal molecules, strong penetrating power, and is flammable and explosive. These characteristics require strict requirements for sealing materials and processes.
As far as sealing materials are concerned, careful selection is required. For example, some polymer materials, although they can be used in ordinary scenarios, may be degraded due to hydrogen penetration. Therefore, it is advisable to choose materials with high barrier properties and resistance to hydrogen embrittlement. Such as special rubber, which has been specially formulated and processed to enhance the barrier to hydrogen and reduce its penetration. Or metal sealing materials, which have been surface modified to improve the resistance to hydrogen erosion.
At the process level, the design of the sealing structure cannot be ignored. It needs to be carefully planned according to specific application scenarios, such as pressure, temperature, medium flow and other factors. For example, in a high-pressure hydrogen environment, the sealing structure must be able to withstand high pressure and ensure that it still maintains a good seal under pressure fluctuations. This may involve the installation of multiple sealing lines, such as combined sealing, internal elastic seals, and external rigid sealing structures, which work together to strengthen the sealing effect.
Furthermore, the inspection and maintenance of the sealing system is the key to ensuring the effectiveness of the sealing scheme. Regularly use professional means to check its sealing performance, such as the use of non-destructive detection technology, to check whether there is any hidden danger of leakage at the seal. If there is any abnormality, repair or replace it in time to maintain the stable operation of the system.
In short, the sealing scheme for hydrogen applications is a system project. From material selection, to process design, to inspection and maintenance, every link is closely linked. Only by considering all aspects and careful planning can we obtain an excellent sealing scheme suitable for hydrogen applications and promote the safe and efficient development of hydrogen-related applications.
Hydrogen is unique and increasingly important in today's applications. However, when it is applied, the sealing business is the most critical, and it is related to many important items such as efficiency and safety.
If you want a sealing solution suitable for hydrogen applications, the first thing to understand is the characteristics of hydrogen. Hydrogen has minimal molecules, strong penetrating power, and is flammable and explosive. These characteristics require strict requirements for sealing materials and processes.
As far as sealing materials are concerned, careful selection is required. For example, some polymer materials, although they can be used in ordinary scenarios, may be degraded due to hydrogen penetration. Therefore, it is advisable to choose materials with high barrier properties and resistance to hydrogen embrittlement. Such as special rubber, which has been specially formulated and processed to enhance the barrier to hydrogen and reduce its penetration. Or metal sealing materials, which have been surface modified to improve the resistance to hydrogen erosion.
At the process level, the design of the sealing structure cannot be ignored. It needs to be carefully planned according to specific application scenarios, such as pressure, temperature, medium flow and other factors. For example, in a high-pressure hydrogen environment, the sealing structure must be able to withstand high pressure and ensure that it still maintains a good seal under pressure fluctuations. This may involve the installation of multiple sealing lines, such as combined sealing, internal elastic seals, and external rigid sealing structures, which work together to strengthen the sealing effect.
Furthermore, the inspection and maintenance of the sealing system is the key to ensuring the effectiveness of the sealing scheme. Regularly use professional means to check its sealing performance, such as the use of non-destructive detection technology, to check whether there is any hidden danger of leakage at the seal. If there is any abnormality, repair or replace it in time to maintain the stable operation of the system.
In short, the sealing scheme for hydrogen applications is a system project. From material selection, to process design, to inspection and maintenance, every link is closely linked. Only by considering all aspects and careful planning can we obtain an excellent sealing scheme suitable for hydrogen applications and promote the safe and efficient development of hydrogen-related applications.
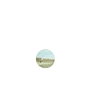
Scan to WhatsApp